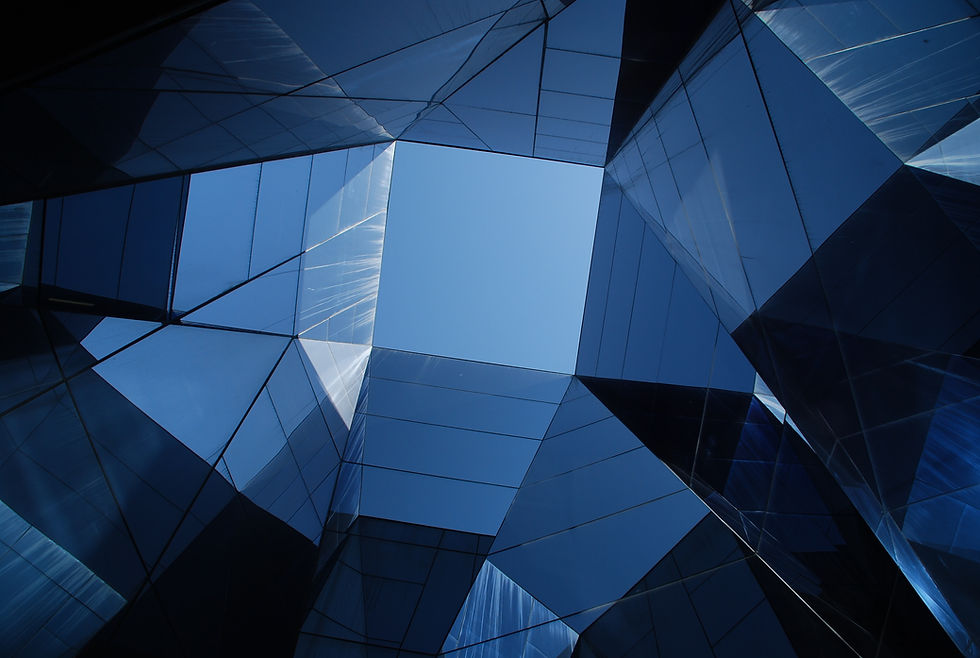
(5S Method Part 5)
Sustain Phase
The objective of this stage is to make sure the 5S process becomes the new normal in the workplace. It can be difficult to get employees adjusted to the new standards and will take effort and diligence to make it a habit for everyone. The sustain phase is here to ensure workers understand what is expected and to stick to them.
Make it clear 5S is permanent
Push the value that 5S is here to stay and it is not just an idea or experiment that will fade away, in order to do this, try these methods:
Have 5S be part of performance evaluations
Adding incentive that following 5S will be recognized helps employees keep this as a standard.
Have a sustain board
Turning the 5S status board into a sustain board will help to keep everyone on track, keep the issues section of the board so there can be constant improvement. Having this board will make it clear that leadership is keeping tabs on the progress of the 5S processes.
Peer inspections
Schedule a time for one team member to evaluate another team member's fulfillment of 5S, this will help employees be accountable and be able to help one another out where there is a shortfall.
Responsibilities
Here are some steps to help employees keep up with their tasks and be vigilant in constantly improving their 5S duties:
Make sure all workers stay on top of cleaning their spaces and taking care of their responsibilities before they leave work.
Plan regular cleanings, include the details of what needs to be cleaned and whose responsibility it is on the status board.
Identify the most efficient strategy used so all teams can implement them.
Have a conversation about upcoming changes and the most productive way to carry them out.
Talk about issues that have arisen and search for the root of the problem in order to solve them.
Have a 15 minute meeting each week to discuss 5S questions and concerns.
Daily Check in
Next to the 5S communications board, include an inspection sheet. This will be used by the supervisors who will then run a one minute inspection each day. If the inspection cannot be completed in a minute, an overview of the visual controls covered in the “standardize phase” is necessary. Make any changes needed for inspections to be quick and efficient. Additionally supervisors should check the issues log during their daily inspection as well as 5S leaders weekly, then address whatever problems are needed.
Auditing
As time goes by after first implementing the 5S process into the work environment, it is easy for workers to start to cut corners and slack off on their responsibilities. In order to avoid this, create an audit team. This team will be in charge of periodically visiting each department, taking snap reviews and doing spot checks. This will create peer based accountability and push each employee to do their best and be proud of their efficiency. It is also important that all management is familiar with the processes and procedures of 5S so they can be involved with improvements and issues that must be addressed.
Comentários